Why do I care?
Well, maybe you don’t.
If you're SURE you're working well below the maximum capacity of your containment AND:
- the thickness of your casting isn’t important
- you’re casting with glass that packs in densely (like a strip bowl)
- your glass is spread evenly across your shape
It may not matter. As long as the glass is thick enough to flow out and level itself (more than 1/4”) and you’re reasonably cautious about your casting and annealing times, your casting will probably come out fine.
In that case, here are a few things you should consider:
- Powders and smaller frits “shrink” more during casting than larger sized frits.
- Annealing and cool-down times increase exponentially with thickness.
- It’s possible to over-fill a shape by piling up too much glass in the middle. This is a way to get nice edges and “flow” effects, but it’s REALLY, REALLY important that the glass doesn’t flow over the top of the fiber.
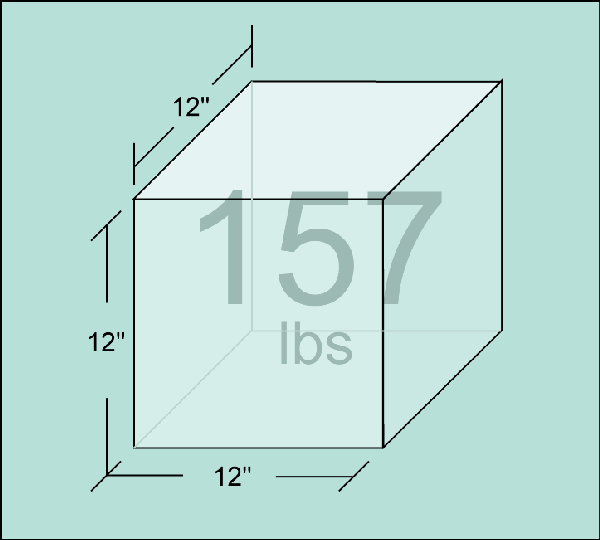
What if it does matter?
Picture a cube of glass one foot on each side. If it’s fusible glass, it probably weighs about 157 pounds. That’s a lotta glass; you probably won't be making this in your kiln anytime soon. This is a valuable number, though. It tells us that the density of fusible glass is 157 pounds per cubic foot, or 157 lbs./ft3.
Here are some more manageable density numbers:
- 0.0936 lbs./in3
- 1.5 oz./in3
- 2.5 g/cm3
Every glass formulation is unique, so different glass colors will have slightly different volumes for a given weight. These numbers are close enough for estimating the weight of the glass needed to fill your casting, though.
You find this weight by determining the volume of your shape (multiply area by thickness) and multiplying it by the appropriate density value.
If you’re a hot calculator jockey, go for it!
The rest of us can use the ShapeCasters weight and volume calculator